The production of laminated insulation materials is becoming increasingly important in today’s industrial setting. With their cost-effective solutions, they provide a great alternative to traditional forms of insulation. Laminated insulation materials are effective for industries ranging from automotive and aerospace to medical and energy.
They offer superior protection against heat, cold, sound, and fire while being lightweight and easy to install or replace. Their long life spans make them an attractive option for any industry looking for reliable yet cost-effective solutions. Moreover, the flexibility offered by these materials makes them suitable for many different applications as well as custom designs that best suit individual requirements. This article will explore more closely the advantages of laminated insulation material production compared with other forms of insulation on the market today.
Market Trends in the Laminated Insulation Industry
The market for laminated insulation materials is ever-growing, as businesses increasingly look to invest in cost-effective solutions. As a result, many companies have taken advantage of the opportunity and are now manufacturing their high-quality products. This has led to an increase in competition among manufacturers, driving prices down while maintaining quality standards. In addition, technological advances have allowed these materials to be produced more quickly and efficiently than before. As such, trends in the industry suggest that production costs will continue to decrease as innovations emerge. At the same time, there is also a growing demand for environmentally friendly options when it comes to insulation material production.
Consumers are becoming more aware of sustainability and are looking for products that meet their needs without compromising on performance or price point. Manufacturers must adapt accordingly by introducing green technologies into their processes or facing potential losses in revenue due to customer preference shifts toward sustainable alternatives. Finally, its worth noting that product development within the laminated insulation sector remains highly competitive with numerous players vying for market share through innovation and design improvements.
Companies must stay ahead of the curve by investing heavily in research & development efforts if they want any chance at gaining an edge over competitors in this fast-paced space. Additionally, creating strong relationships with customers can help ensure success as loyalty programs may provide exclusive access to certain features not available elsewhere on the market
Challenges and Opportunities for Producers of Laminated Insulation Materials
The production of laminated insulation materials presents both challenges and opportunities for the industry. On one hand, the cost of producing such materials is a significant factor that must be considered when evaluating the success of an operation. On the other hand, there are numerous ways to create cost-effective solutions while still maintaining high standards in terms of quality control. For example, producers can look into capital investments in technology and automated processes as well as explore new suppliers with better pricing models or alternative raw material sources.
Additionally, producers should explore innovative ways to reduce waste during production which could result in increased profitability and efficiency. Another challenge is overcoming market saturation where competition increases due to a large number of players entering the market with similar products at varying price points. In this situation, producers need to differentiate themselves by providing value-added services such as improved customer service or developing specialized product lines for niche markets that meet specific needs not available elsewhere.
At the same time, these strategies also offer potential benefits including increased sales volumes from repeat customers if done correctly. Overall, many factors should be taken into account when producing laminated insulation materials; however, navigating through them effectively can lead to great rewards for any producer who invests in research and development accordingly.
Innovations in Manufacturing Processes to Reduce Costs
Manufacturing processes are essential for producing laminated insulation materials and reducing costs in the industry. To maximize efficiency, businesses must invest in innovative solutions that can improve their production capabilities while still maintaining cost-effectiveness. Solutions such as automation, advanced equipment, and updated production methods can help to reduce the time and labor needed while also increasing product quality. Automating parts of the process or using robotic systems is one way to minimize labor costs while ensuring consistent results with every batch produced.
Additionally, investing in new machinery and technologies that allow for faster production cycles will enable companies to produce higher volumes of material at a lower cost per unit. Finally, updating existing processes by utilizing lean manufacturing principles can further streamline operations and decrease waste associated with traditional approaches. By making use of these cutting-edge solutions manufacturers can ensure they’re staying competitive in the market without sacrificing quality or profitability
Key Considerations When Choosing a Manufacturer
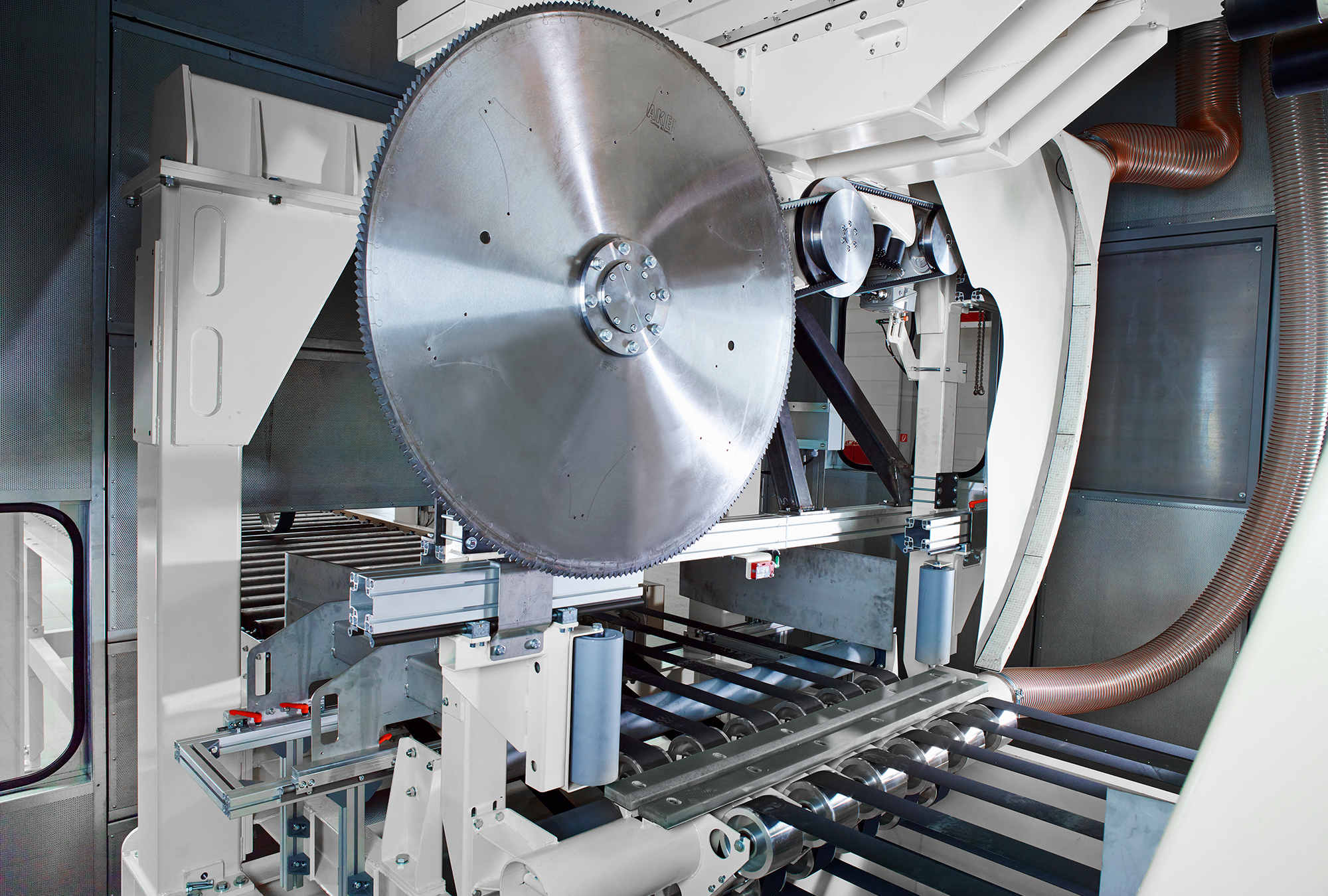
When it comes to selecting a manufacturer for the production of laminated insulation material, there are several key considerations. Quality is paramount to ensure successful project completion and customer satisfaction. Manufacturers must have a proven track record of quality assurance processes and use only certified materials that meet industry standards. Additionally, they should have access to advanced technologies, enabling them to produce high-quality products quickly and cost-effectively.
Price is also an essential factor when choosing a manufacturer; therefore one must be aware of any hidden costs or additional fees associated with the production process such as shipping costs or minimum order requirements. Furthermore, manufacturing capabilities should be taken into account as some companies may specialize in particular types of laminated insulation material while others may offer more flexibility in terms of size and shape options. Lastly, understanding turn-around time expectations can help identify whether the selected manufacturer will be able to complete projects within the desired timeframe or not.