The automotive industry has been transformed by the introduction of electric vehicles, and metalworking is no exception. As traditional manufacturing techniques are being challenged to keep up with the changes in technology, press brakes have emerged as a powerful tool for producing components for these new vehicles.
In this article, we will explore how press brake technology has advanced to meet the needs of modern electric vehicle manufacturers and discuss how it can help shape the future of metalworking. Well also look at some examples of successful applications and see why they make such an important contribution to automotive production today.
Analyzing the Benefits of Press Brake Machining in EV Production
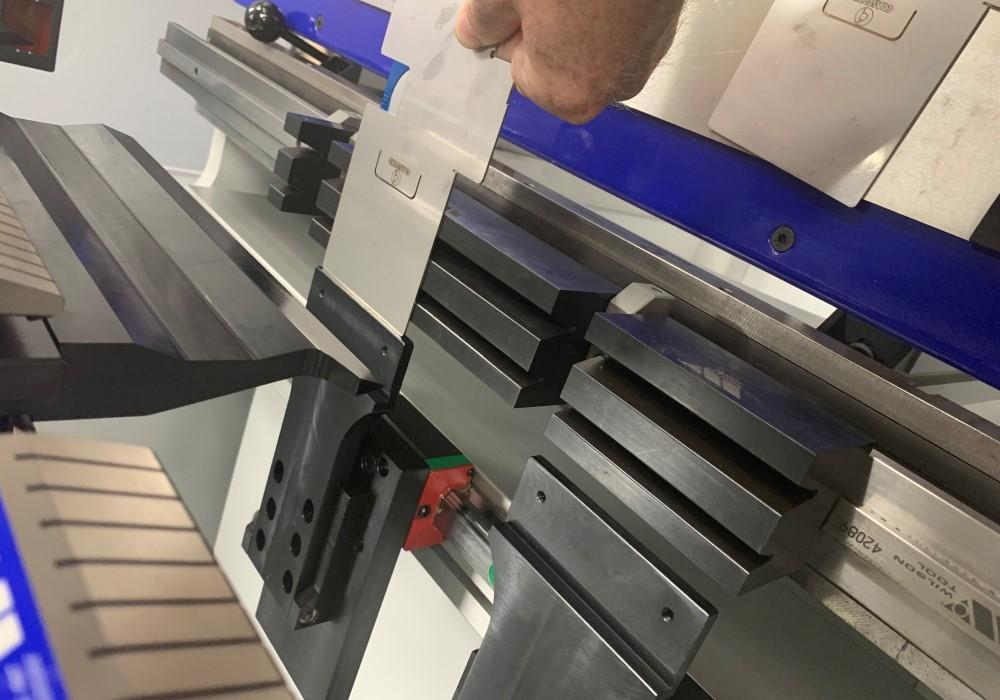
Press brake machining is an essential technology in the production of electric vehicle (EV) components. Its use enables manufacturers to achieve greater precision and accuracy than with traditional metalworking techniques, while also reducing costs and time needed for production.
Through press brakes, parts can be bent into complex shapes without manual labor or costly machines. This makes it easier to create custom-designed components for EV applications, such as chassis frames and battery enclosures.
Additionally, press brake machining allows for a higher degree of quality control over finished products due to its ability to produce uniform bends that meet exacting standards. The benefits of using press brakes in EV production extend beyond cost savings and accuracy.
By tapping into automated manufacturing processes, press brakes offer greater speed and consistency when producing components at scale – something that’s increasingly crucial as demand grows for EVs across the world. With its flexibility comes additional opportunities: presses can be reconfigured quickly to accommodate new designs or materials used in EV construction, minimizing disruption during product changes or updates.
Analyzing the potential gains from adopting press brake machining into electric vehicle production reveals significant advantages over traditional methods of fabrication – from improved efficiency and decreased costs through faster cycle times and better part quality assurance – making it an ideal choice for those looking to optimize their operations in this rapidly evolving industry.
Exploring New Technologies for Increasing Efficiency in Electric Vehicle Components Manufacturing
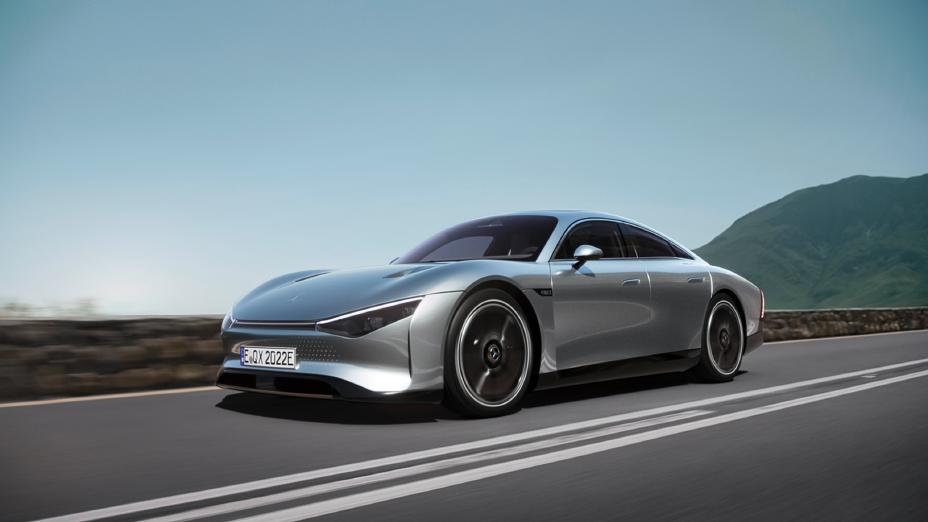
The evolution of electric vehicle components has led to the emergence of new and innovative technologies for increasing efficiency in manufacturing. Press brakes, which are machines used to bend sheet metal into desired shapes, have become increasingly popular among manufacturers due to their ability to quickly produce high-quality parts with extreme precision.
These machines utilize unique algorithms that allow them to adjust the force applied to the workpiece to achieve precise bending results. Additionally, they come equipped with a variety of sensors that help ensure accuracy during production.
In addition to press brakes, advanced laser cutting systems are also being implemented by many manufacturing facilities as an efficient way to cut complex shapes from metals or other materials. With laser cutters, intricate designs can be created without additional time spent hand-finishing edges or surfaces – resulting in faster and more cost-effective production times for electric car components.
Furthermore, 3D printing technology is now being used by some companies when creating custom parts that require intricate detail and design elements not achievable through traditional methods such as machining or injection molding. As electric vehicles continue their rise in popularity around the world, manufacturers must remain at the forefront of innovation when it comes to producing these components efficiently and accurately while maintaining quality standards throughout every stage of production.
Utilizing these newly available technologies will play a major role in helping businesses stay competitive within this growing industry while providing customers with reliable products backed by long-lasting warranties or guarantees
The Future of Beyond Traditional Metalworking: Leveraging Automation and Innovation for Increased Productivity
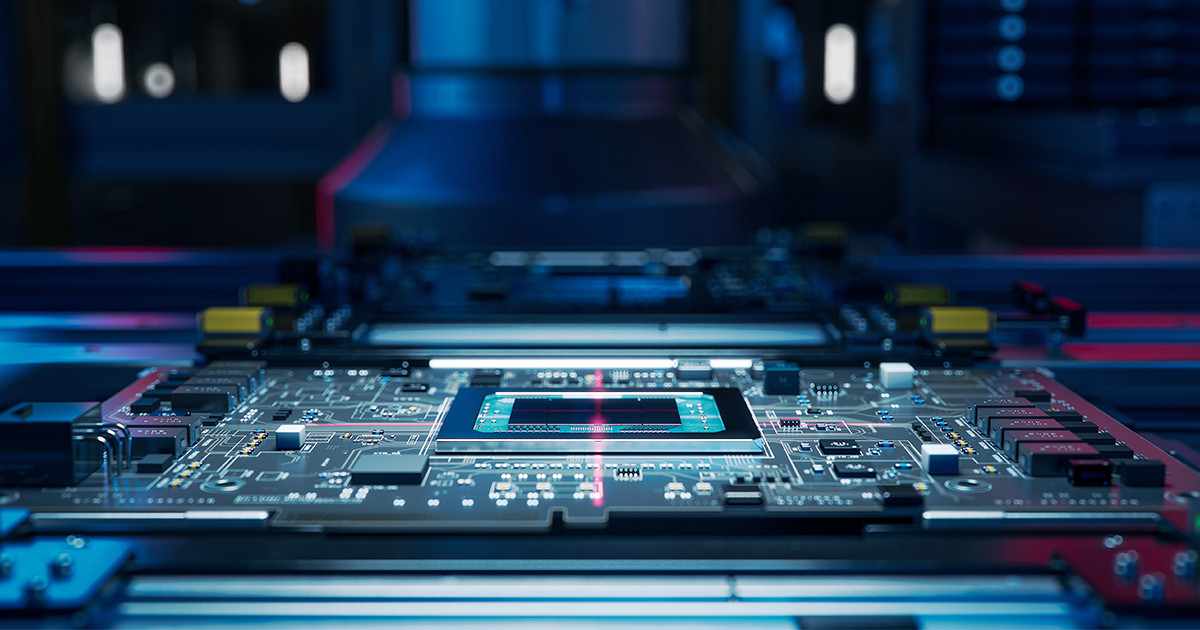
The future of traditional metalworking is evolving rapidly, and automation and innovation are the driving forces behind this evolution. Automation has allowed for advances in production line efficiency that have drastically reduced labor costs while increasing productivity.
Meanwhile, innovative new technologies have made it possible to produce components with unprecedented levels of precision and accuracy. Together, these developments are helping to revolutionize metalworking processes used in the automotive industry by allowing for faster turnaround times and higher quality control standards. As electric vehicles become more prevalent on roads around the world, their components must be produced at a quicker rate than ever before – something that automation and innovation can make possible when combined with modern press brakes technology.
The combination of automated manufacturing processes alongside technological advancements in press brake equipment means increased productivity, improved safety measures, better quality control systems as well and decreased lead time for component production – all leading toward a brighter future beyond traditional metalworking.
Conclusion
The press brake machine is an incredibly versatile and important tool in the metalworking industry, from its roots in traditional components to its evolution of electric vehicle components. Its combination of precise cutting angles and consistent pressure makes it a perfect choice for automotive manufacturers looking to create parts that are both aesthetic and strong.
Through innovations like automated systems and computer-aided designs, press brakes have become invaluable for creating products with more accuracy than ever before. As technology continues to advance, press brakes will remain an essential part of the auto manufacturing process for many years to come.