When it comes to printed circuit board (PCB) assembly, there are two main techniques used: surface mount and through-hole. Both methods provide a reliable way of connecting electronic components on the PCB but offer different advantages.
This article provides an overview of both techniques so that readers can make informed decisions about the best option for their next PCB project. Surface mount technology (SMT) is a popular choice among electronics engineers as it offers higher density and smaller footprints than traditional through-hole components.
SMT uses small pads or lands on the surface of the board instead of drilled holes, making them suitable for automated pick-and-place machines which significantly reduces overall production time and cost. Additionally, SMT components have great electrical characteristics such as high current capacity, low inductance, and good thermal dissipation capabilities which makes them ideal for high-speed applications like computer networking and telecoms equipment.
Through-hole mounting has been around since before World War II when manual soldering was used to connect wire leads to create complex circuits with discrete electronic components such as transistors or diodes. Through hole construction larger parts with longer pins to be securely mounted into place without fear of vibration damage due to its robustness compared to other methods of assembly.
Also, unlike SMT devices where heat may cause damage during wave soldering processes, through-hole assemblies are usually unaffected by this process allowing boards with large populations of mixed component types including connectors and switches -to be reliably produced at a lower cost. Overall, Surface Mount vs.
Through Hole technologies each offer unique benefits depending upon application requirements; however, both options have become increasingly important in today’s world of miniaturization where reducing size whilst maintaining performance is often essential.
Advantages of Surface Mount Technology
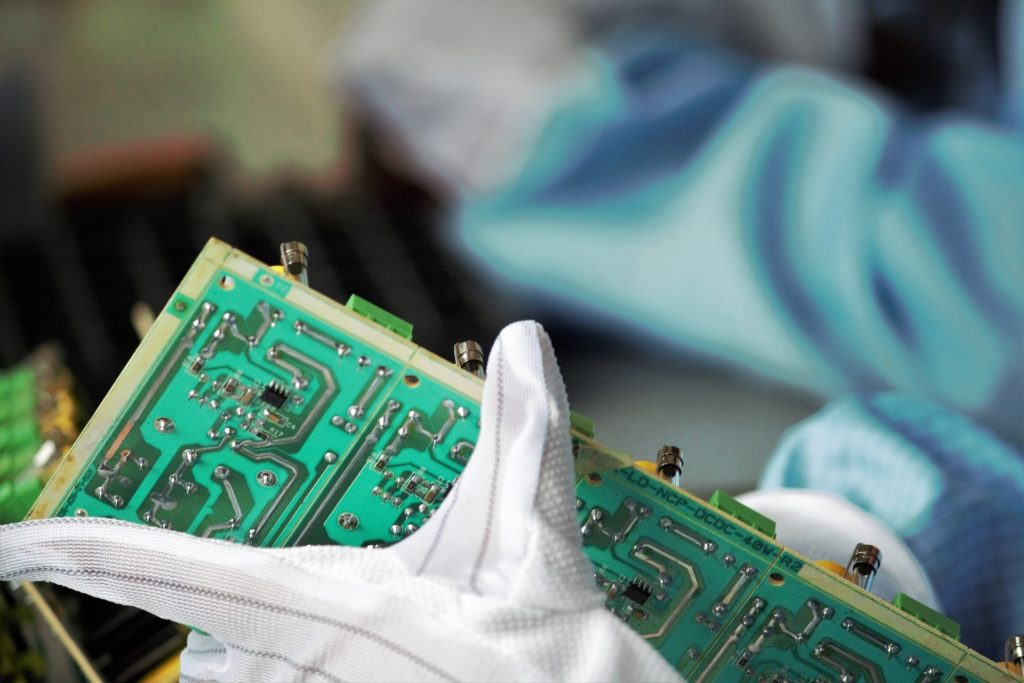
Surface mount technology (SMT) is a type of PCB assembly technique that has several advantages compared to traditional through-hole techniques. SMT offers improved electrical performance, faster production speeds, smaller physical size, and less weight.
The main advantage of using SMT is its increased circuit density, or the ability to place more components in the same area as with through-hole methods. Additionally, because no holes are drilled into the board during assembly, there is less risk for shorts due to improper soldering or component lead misalignment.
Another benefit of SMT is that it can support both single-sided and double-sided printed circuit boards with greater efficiency than through-hole techniques. By utilizing surface mount devices on both sides of a board as well as finer-pitched leads and pads, designers can achieve higher levels of complexity without increasing board size or cost significantly.
Finally, SMTs require little manual labor which lowers costs and increases overall production speed compared to other types of PCB assembly processes.
Disadvantages of Through-Hole Technology

One of the key disadvantages of through-hole technology is its relative complexity compared to surface mount. Through-hole components require more labor and precision for them to be soldered properly, as the leads must pass through the holes in the PCB and then be soldered on both sides.
This process can increase assembly time significantly, making it less cost-effective than surface mount techniques. Additionally, since these components protrude from both sides of a board they tend to take up more space than those securely placed on one side.
This makes it difficult or impossible to use this technique when boards are densely populated with components or designed for compact applications such as handheld electronics and other consumer products. Finally, rework capabilities with through-hole assemblies are also limited due to their size and shape which can make repairs costly and time-consuming for manufacturers if solder joints become damaged during assembly or after installation.
Cost Considerations for Both Systems
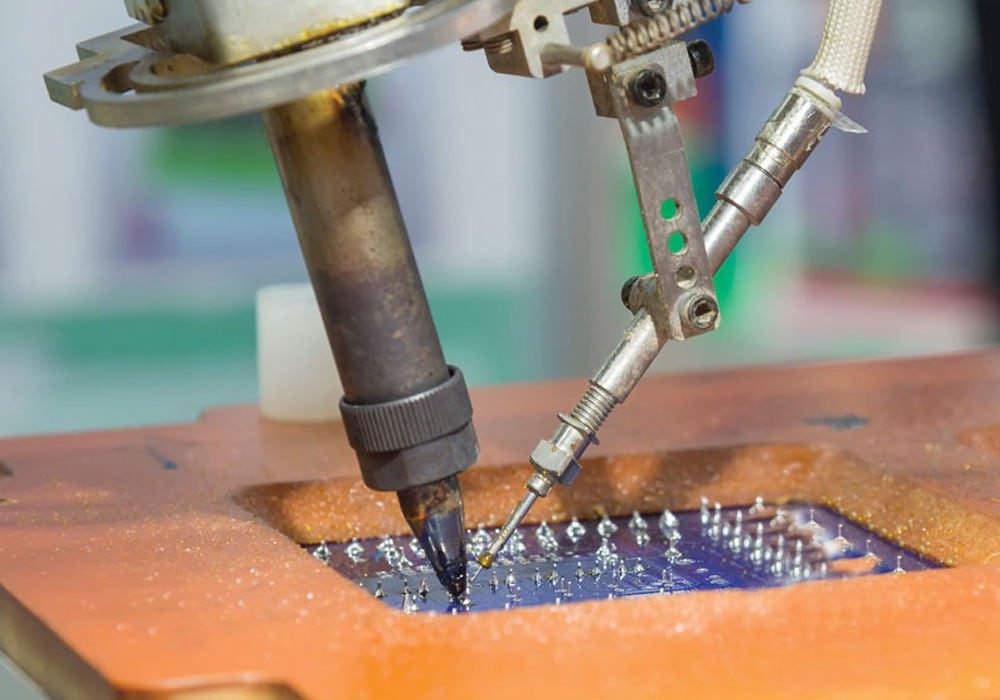
Surface mount and through-hole assembly techniques are both routinely used in printed circuit board (PCB) manufacturing. While each has its advantages and disadvantages, cost is a major consideration for engineers when selecting an assembly technique.
Surface mount technology (SMT) often requires lower material costs due to the smaller size of components, while through-hole assemblies may require more parts to be soldered onto the PCB. Additionally, SMT may require higher labor costs since it typically takes more time to assemble surface-mounted components than traditional through-hole components.
On the other hand, some complex boards with high component densities can benefit from using SMT since it allows for tighter packing of components without sacrificing performance or reliability. Ultimately, cost considerations must also take into account factors such as production volume and throughput rates when determining which type of assembly technique will produce the best outcome at an acceptable price point.
Industry Trends in PCB Assembly
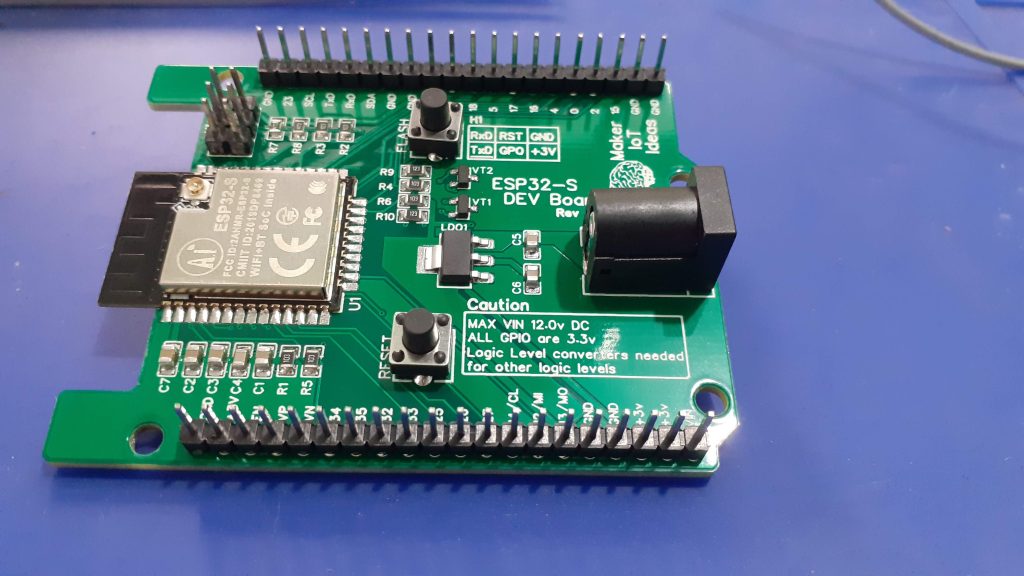
Recent advancements in technology have made printed circuit board (PCB) assembly easier and more efficient than ever before. As a result, manufacturers can respond quickly to industry trends and produce products with greater reliability and shorter lead times than ever before.
This article will explore the two most common PCB Assembly techniques: surface mount technology (SMT) and through-hole technology (THT), as well as current industry trends for each technique. Surface Mount Technology has become increasingly popular due to its ability to reduce the size of assemblies while increasing their functionality.
SMT uses smaller components that can be placed directly on the surface of the board without drilling or soldering, resulting in faster production cycles, higher throughput rates, increased yields, reduced labor costs, improved reliability, and performance results. The trend towards miniaturization is only expected to grow in this sector as designers seek out new ways of packing maximum power into minimal space requirements.
On the other hand, Through-Hole Technology remains an important part of modern PCB assembly processes due to its ability to accommodate larger components that would not fit onto an SMT board design. THT allows engineers more flexibility when it comes to designing custom boards with specific component needs that may exceed those achievable using SMTs alone.
Increasingly complex tasks such as creating high-density interconnects (HDIs) require both methods working together within a hybrid approach — something many leading companies are already taking advantage of today for superior results. Overall, both Surface Mount Technology and Through-Hole Technology remain essential parts of any successful PCB Assembly process; however, there is no one-size-fits-all solution when it comes to choosing which technique will best suit your project needs – careful consideration must always be given depending on individual product specifications and goals desired from each build cycle before selecting either method over another
Conclusion
Surface Mount and Through-Hole assembly are two common PCB Assembly techniques used in circuit board manufacturing. Both have their advantages and disadvantages, depending on the type of project being worked on.
The choice between these two methods will depend upon several factors such as cost, complexity, size, component availability, and flexibility. With an understanding of both techniques, it is easier to make the right decision for any given project.
Ultimately the choice comes down to what works best for your particular application.